Failure Analysis at Sea (June 2-6, 2023)
- kenyon sprague
- Jun 6, 2023
- 7 min read
A couple Ibuprofen, and we were feeling not too bad after yesterday's thrash of same-day muffle
removal, repair and re-installation. We exited Milwaukee again, and headed south bound for Waukegan, about 60 miles closer to Chicago where we were due to meet our Chicago relatives and my parents on Saturday and Sunday. I checked the muffler carefully once we were underway. It looked fine, but upon closer inspection, I noted that the sides of it were pulsing.
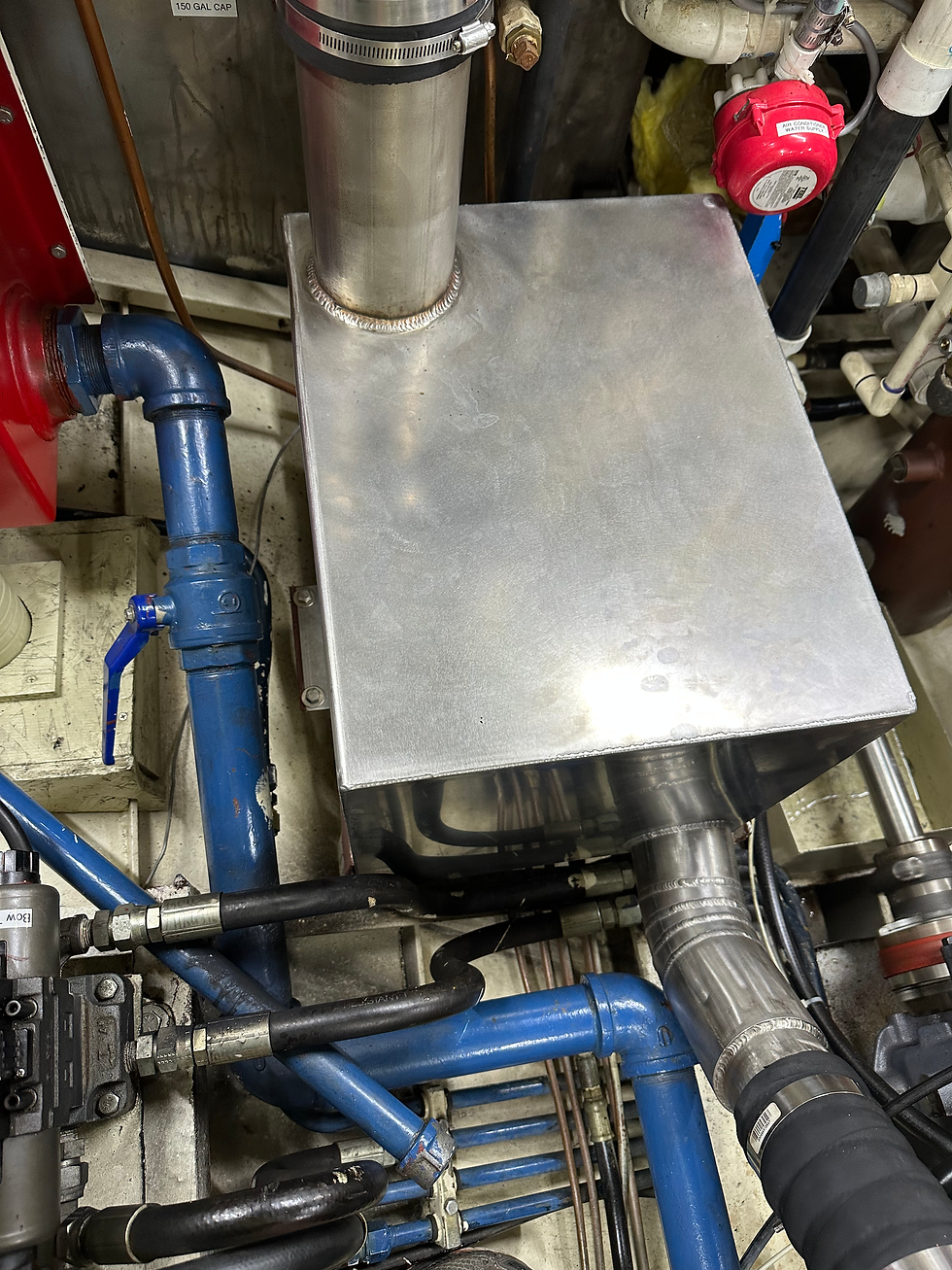
A water-lift muffler is just a box with two pipes. Diesel exhaust fumes from the turbo and lake water from the engine cooling heat exchanger are mixed and pour into the muffler through the curved front pipe, then the exhaust pressure pushes the water and fume mixture uphill about 30 inches through the top pipe where it all exits the transom of the boat just above the waterline. The muffler has twin benefits of keeping the exhaust very cool, and very quiet. 30" of water height equates to only about 1 psi, but multiplying that by the area of each side means that there is a force of several hundred pounds pushing outward, and the individual piston exhausts may amplify that force considerably, especially if the engine is running at a resonant frequency of the muffler. Even pushing my hardest in the middle of the muffler side, I couldn't see the metal deflect, but underway at 1600 rpm, I could clearly see the sides bow out, then in, about twice per second. It didn't bow much, maybe only a millimeter or so, but it was obviously vibrating.
Yesterday's leading theory was that we just had a bad weld, insufficient penetration, or a discontinuity - happens all the time, even at good shops with skilled personnel. But after seeing that visible bowing of the sides, all I could think about was the possibility of fatigue failure. I shared this theory with Lori and we started worrying more about having a second failure. [Lori: 'Worry' does not capture the emotion I felt as we motored ever further from the safety of home port. Jim is good at designing useful stuff but he's REALLY good at failure analysis and his fatigue theory was making way too much sense. I was convinced another failure was inevitable, but when? Cue the music--"Pop Goes the Weasel"--and now I am reliving my childhood trauma just waiting for that scary clown to pop out of the box.]
I happen to know a bunch of good metallurgists, so I called a couple. What I learned was that 1) 1/8" thick 304 stainless is basically the go-to material for mufflers and similar applications. 2) Bad welds happen all the time, and is a likely candidate for having caused the event yesterday. 3) my hare-brained idea to use blocks and web straps to make all the sides slightly concave and reduce the fully reversed bending behavior I was convinced was happening at each edge was likely to cause more problems than it would solve. 4) We can't yet rule out fatigue and/or defective muffler design, and the safe thing would be to not try to cross Lake Michigan with 2 octogenarians aboard until I have the failure mode positively identified and fixed.
Lori and I thought hard about canceling on my relatives, but kept on our south heading towards Chicago. Then I went below for another visit, and the decision was made for us. Upon opening the door, everything looked good, no diesel smoke, but wait! Is that water squirting out back there? By golly, we had another leak, this time at the bottom aft edge. It was gushing out good, but again, the bilge pumps were keeping up with the flow with no problem. We weren't going to sink, and even if the bilge pumps failed, we could just shut down the engine and close all the thru-hull valves while we waited for the humiliation of being towed in to port. Since the latest cracked weld was at the bottom of the muffler, the leak was submerged within the muffler box and no diesel fumes were escaping to fumigate me, a small favor for which I was grateful. Two weld failures on two different edges of a brand new muffler, both within 12 hours of installation... conclusion: Fatigue failure... the muffler sides were flexing too much and too many times in response to system vibration and had overstressed the edge welds.
Defeated, I climbed the stairs and told Lori we had broken the boat again. She sighed, and immediately changed course for Racine, Wisconsin which was only 10 miles away. I radioed the marina and asked for an easily accessible dock since we were taking on water, which they promptly assigned. We got in no problem, shut down the engine and the leak stopped. Then we again began the task of cancelling reservations and trying to find a welder in a strange town. The first call was to Smith's welding, where Tim picked up and sounded game for the challenge. Same drill, we wrestled the damn box out, dumped it into a cart and wheeled it to the parking lot where Tim (who has an art & sculpture degree, but found that welding pays better) coaxed it into his aging Camry's trunk. He understood the issue and happened to have sufficient 1/8" 304 stainless on hand from an old job. A cube has 12 edges and 6 faces, our box was made of 2 U-shaped sections with radiused bends forming 4 of the 12 edges. We asked Tim to reinforce the remaining 8 edges with external angle brackets, thus doubling the wall thickness at every welded edge, and simultaneously stiffening every face such that any vibrational amplitude will be reduced, and all the natural frequencies of the muffler will be significantly raised, hopefully well out of range of whatever our diesel and/or coolant exhaust system is generating. At Tim's suggestion, we agreed he should also re-weld all of the original welds (before covering them with new L-brackets) as they probably all had incipient cracks already propagating through them, they just hadn't yet had their turn to completely fail yet.
Tim got to work immediately, but it was clear that we weren't going to get it back till the next day (I calculated he needed to run a total of about 43 feet of weld!), and that it would then take us plenty of time to reinstall a heavier and slightly larger muffler in the old brackets. We had to cry Uncle, and notified our family that we had failed, the Perseverance would not make it to Chicago in time to keep to our plans.

Saturday late morning saw Tim delivering our muffler back to us (I know he was still working on it at 3am) along with some requested shims. We cut him a check and trudged back to our blue boat with a no-longer beautiful stainless steel muffler. The formerly sleek and shiny expensive box (that I actually POLISHED before first installing it) was now a FrankenMuffler. Stout reinforcing brackets were welded on speedily and solidly, not beautifully, and a stiffening girdle was on several of the most vibration-prone faces. In preparation for the larger box, I used every erg of strength I possess along with a pair of cheater bar enhanced pipe wrenches to pry the receiving brackets just a tiny bit wider in hopes it would still slide in. Tim also shaved down the lower edges of the muffler with an abrasive disc to gain me a few precious fractions of an inch. I fashioned rope handles to aid in maneuvering the beefier muffler down the stairs and around all the corners. This was the 7th time I've moved a muffler through those stairs, and I think it was the hardest. Somewhat amazingly, it all worked, and the 1/8" of remaining clearance between the box and the rails was sufficient. Even more amazingly, neither of us bled or got injured, though I've got some sore ribs from awkwardly laying over the muffler to get the last bolts tightened and we're both a bit stiff from the exertions.
We were just finishing our shims, when somebody knocked on the hull - turns out that since we failed to make it to Chicago, some of my relatives pitied us and drove up to Racine to see us! We had a nice (but quite brief) visit with my sister, her husband and Ella, my niece (on leave from the USCG academy). Ella performed a safety check of our vessel, but tragically, forgot to test the horn before they had to run off. After that, we got everything bolted back together, ran the diesel for a bit, saw no problems, and called it a night.
Conclusion: My metallurgist friends tell me that 12 hours of 2 Hz vibration = nearly 100,000 cycles, generally considered the start of the high-cycle fatigue regime. The box becoming slightly spherical, then slightly concave twice a second that many times puts a lot of fully reversed bending stress right in the center of the edge weld bead, where it fatigue fails leaving a hairline crack. Tellingly, the hairline cracks were both perfectly centered on their respective edges, the cracks petering out as they approached the much stiffer corners of the box where the flexing would be less. My new welder friends both told me that the muffler looked like a good design to them, that the fabrication shop clearly knew what they were doing, and that's how they would have done it too. But it's now looking like it WAS a defective design, one that I specified to have built. To be clear, "my design" was simply, "here's the old rusted out 3/16" steel box that fits and has worked fine for 30 years, please make me a shiny new one of 1/8" 304 stainless with exactly the same exterior dimensions." 304 stainless has considerably higher strength, so making the box out of thinner gauge seemed reasonable, and several experienced boating and fabrication people I talked to concurred.
I should feel more shame, but I'm pretty convinced that it was a reasonable design, just not for this boat. Perhaps if the Perseverance ran with a little different gearing, it would never have resonated at just the wrong frequency for the new muffler, and no problems would ever have developed. I'm not going to do the simulation work to figure that out, I'm just hoping that the new uglified version is now so stiff and overbuilt that this muffler WILL NEVER HAVE TO COME OUT OF THE BOAT AGAIN.

Epilogue: We ran for twelve solid hours yesterday in calm seas and five harrowing hours today in 4-5' waves and the redesigned/reinforced muffler seems to be working fine. Crossing our fingers that this is the end of the muffler saga.
Comments